Arnreiter
Drive Systems provide conveying power in Grain Mill
In grain mills, NORD drive solutions are used for fans and blowers, rotary dischargers, bucket elevators, and other conveying machinery. Due to the presence of finely ground grains and seeds, such applications require explosion-protected systems.

Focus on the Customer
Based in Wallern, Austria, Arnreiter Mühle GmbH produces processed grains and oil seeds primarily for customers in the food industry. A family enterprise founded almost 200 years ago, Arnreiter is fully committed to sustainable production: the mill processes crops grown in the region and strives to use as little resources as possible in production. The site even has its own water mill that generates some of the required energy.
Focus on the Project
In the most recent retrofit of milling and processing systems at the long-established Arnreiter Mühle in 2009, Swiss process technology specialist Bühler installed various state-of-the-art machines featuring NORD drive solutions. The operation with a connected load of 1,400 kW is capable of
- milling up to 80 tons of grain per day and
- further processing up to 20 tons of milled grain per day.

Project Challenge
At Arnreiter Mühle in Austria, grain is milled as well as refined in various processes. This highly automated mill utilizes a wide range of machines for steaming, flaking, crushing, grinding, extruding, roasting, cooling, drying, and peeling. Through these treatments, the shape and characteristics of grains and seeds are changed to improve storage life, digestibility, and baking properties, and to reduce bitterness.
Extensive conveying systems. – A variety of conveying systems featuring flexible drive solutions is required to achieve an efficient transport of particulate and free flowing media from one processing stage to the next. As a company that is fully committed to sustainable production, Arnreiter sought to install robust, low-maintenance drives that would provide a long service life as well as ensure highly reliable continuous operation to safeguard excellent quality of the end products.
Dust hazard. – As raw materials are finely ground, the atmosphere throughout the mill is enriched by dust particles. Electrical drives must therefore be explosionproof. Drawing on a versatile portfolio of mechanical, electrical and electronic drive technology certified for use in hazardous areas, NORD DRIVESYSTEMS was able to provide various different types of geared motors as well as integrated mechatronic drive systems for distributed operation.

Application Solution
NORD geared motors drive belt and bucket elevators that take raw materials from silos on the upper floors to processing machinery elsewhere in the mill. Process media are then fed through a pipe system with a total length of 2,500 m. The low-density fraction comprising small hard particles, dust etc. is removed from the grain in an air-recycling aspirator and taken out by a screw conveyor. Rotary dischargers ensure proper volumetric dosing of products. Micro dispensers allow for adding small components.
Highly durable design. – All of these material conveying and distribution systems are also equipped with NORD geared motors. “They are performing reliably in continuous operation at our mill,” says Martin Rachbauer, Maintenance Specialist at Arnreiter Mühle. Thanks to superior manufacturing quality, NORD drives require only minimal maintenance.
Comprehensive explosion protection. – NORD supplied Arnreiter with various category 3D drive units for use in ATEX zone 22. These included geared motors as well as integrated mechatronic systems for distributed operation, i.e. geared motors fitted with local drive controllers. NORD provides explosion protection solutions for drive systems as a whole, offering both geared motors and locally installed or cabinet-mounted frequency inverters in explosion-proof versions. Every month, NORD manufactures and delivers some 1,500 dust or gas explosion-protected drivesystems suitable for ATEX zones 1, 2, 21, and 22.
Ochrana pred výbuchom plynu
Motory do výbušných prostredí
Ochrana pred výbuchom prachu
Motory do výbušných prostredí
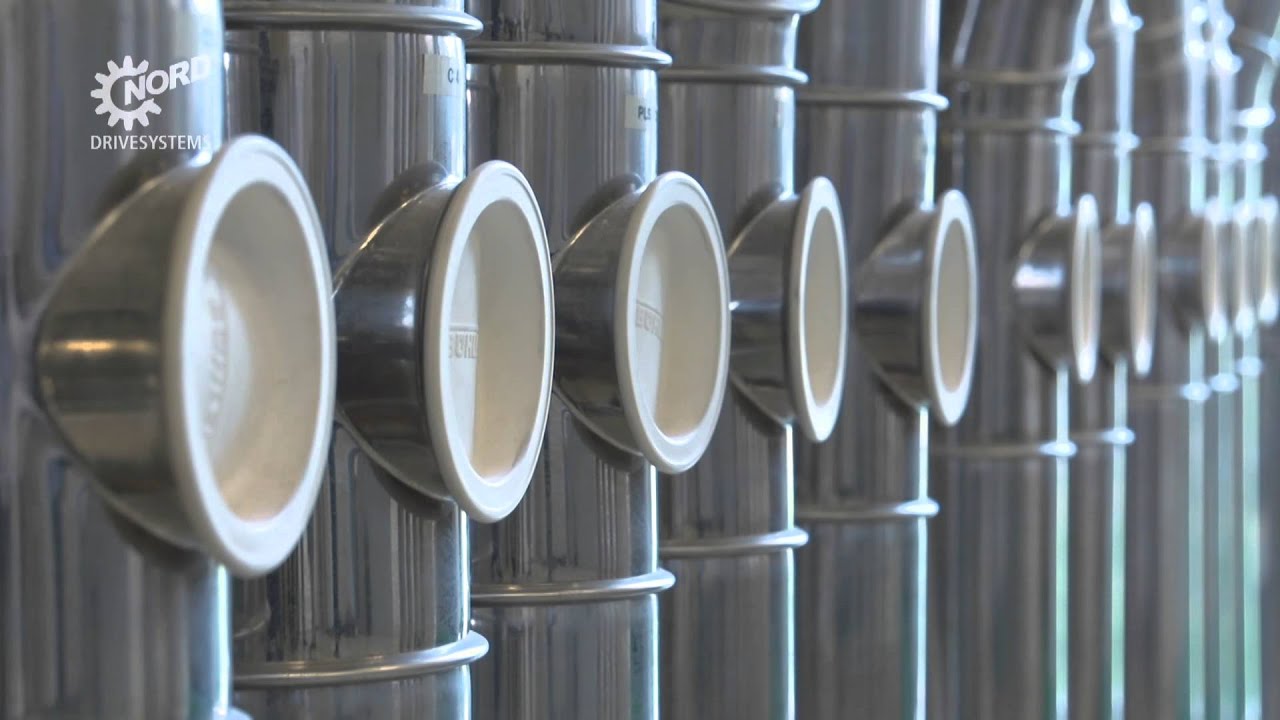
Find further information here: