Motor technology: Which parameters influence efficiency?
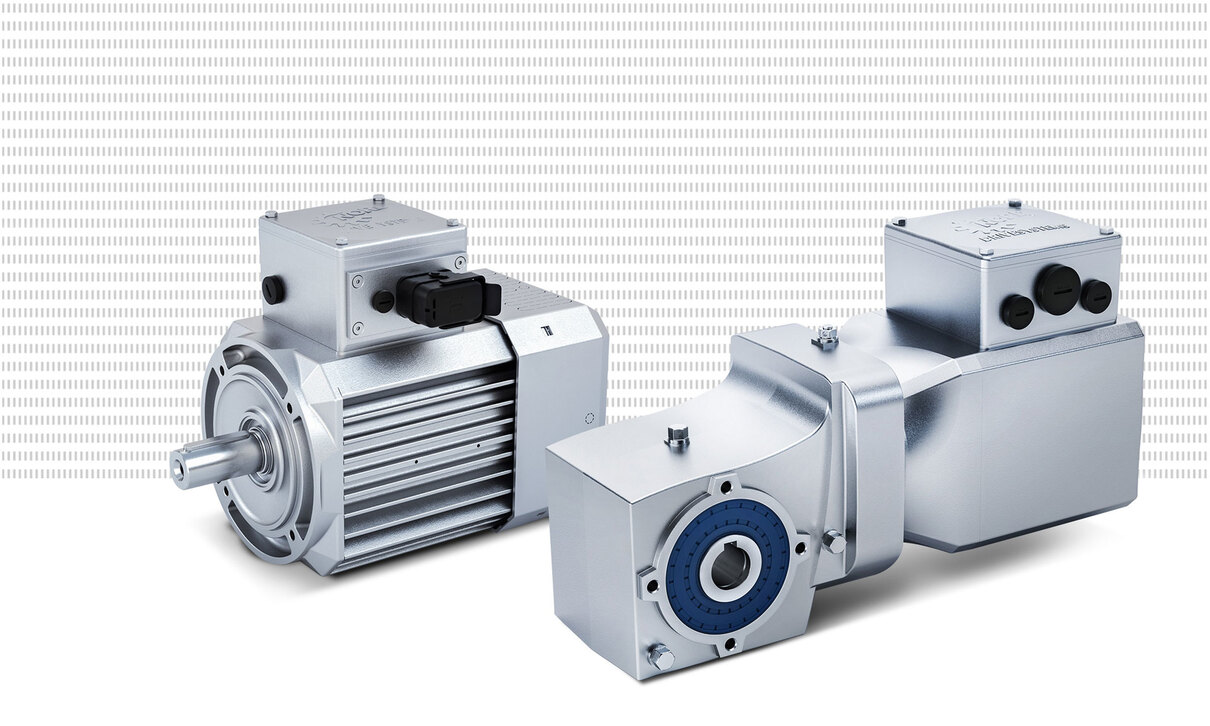
With regard to energy savings, the entire drive system including electric motor, gear unit and drive electronics must be taken into account. Here, the potential is typically between 30 and 60%. In this post, we want to have a specific look at the options for electric motors. NORD DRIVESYSTEMS has been committed to this task since the start of the energy debate several decades ago and attempts to reconcile sustainability, improved economy, higher energy efficiency as well as optimized functionality and performance in all new and further developments of its drive systems.
Based on official OECD numbers, the industry has made the largest contribution in regard to energy savings through improved energy efficiency, amounting to 51% between 2000 and 2017. The largest proportion here is due to generation of process heat and the use of electricity for drive units. Decisive measures in both sectors make considerable contributions both to saving resources and achieving climate targets. Electric motors are the most relevant product group in regard to the Ecodesign Directive, especially for industrial energy consumption, since systems driven by electric motors consume about 70% of industrially used electric energy. This is approximately half of the total electrical energy used in the European Union. According to estimations, electric motors converted about 1,400 terawatt hours of electrical energy into mechanical energy and heat in 2015. Because of this, regulations for electric motors which are in continuous operation exist almost everywhere in the world and in many regions there are even system-related regulations which also include machinery such as pumps, fans or air compressors. Regulation of energy efficiency has an equal effect both on the saving of resources and economic efficiency. Usually, all electric motors which are supplied according to the present regulations (e.g. IE3), including those which are operated continuously in single shifts, recoup the extra investment costs within a short time when compared to previously common IE1 motors On its website, NORD DRIVESYSTEMS provides an up-to-date overview of the globally applicable efficiency regulations and standards for motors.
The First Efficiency-driven Optimization Wave
The first major step towards increasing energy efficiency had to be taken by motor manufacturers in preparation for 2011, when the Directive 640/2009 valid until 30 June 2021 came into force and bindingly specified the use of IE2 motors for continuous operation. Within a year, this doubled the number of IE2 motors in use, while the use of IE1 motors decreased dramatically. For the first time, a significant number of IE3 motors were sold, however their sales only increased when their use became mandatory above 7.5 kW in 2015, and for all powers since 2017. With the new EU 2019/1781 Regulation that has been replacing the earlier provision since 1 July 2021, a considerable decrease in the sales of IE2 motors is to be expected perspectively, because users will use cheaper IE1 motors for applications where the upcoming IE3 regulations do not need to be complied with.
The losses of IE3 motors are about 20% less than those of IE2 motors. In most cases this is associated with major changes, i.e. increase of the active material. Manufacturers responded to this in various ways: Some of them chose a fundamental change in diameter. This has a quadratic effect on the size of the rotor surface as an important key utilization figure. This avoided length extensions or large changes in iron quality. Many manufacturers were unwilling to make the investments, which were associated with this step: Development costs, new aluminum housings with lower rib heights and tendency to a rectangular outer shape, more space for the iron package, same installation dimensions with larger centering, and new bearing covers and fans or fan covers. Some manufacturers exploited the last millimeter of volume, achieved IE2 by compacting the package and winding density and then considered new measures for the step to IE3.

Achieving Efficiency Class IE3 with More and Higher-value Active Material
With the requirement for saving 20% of IE2 motor losses, many asynchronous motors reach their physical and to some extent economical limits. For some motor sizes this means that manufacturers must use the far more expensive copper rotors in order to avoid an increase in size. For gear unit attachment, the IE3 motor means that the flanges are subject to greater loads due to the heavier motor. In the middle of 2021, in the area of application of the EU Ecodesign Directive the legal possibility of “circumvention” of the use of IE3 motors by the use of IE2 motors in combination with frequency inverters was eliminated. For this reason, sales of IE3 motors greatly increased. This also applies to 2-, 6- and 8-pole motors, even if the figures are much lower than for 4-pole versions. For powers from 75 to 200 kW a new direction was included in the Directive for 2023: The IE4 class will also become a reality for standard asynchronous motors with higher powers. Efficiency increases with size. Because of this, the differences between IE3 and IE4 motors can be physically achieved more easily and with fewer modifications.

From Permanent Magnet Rotor to Toothed Coil Winding
Achieving further efficiency with small motors is usually only possible by means of concept changes. NORD DRIVESYSTEMS is deliberately pursuing the policy of 4-pole IE4 synchronous motors, which can be operated with frequency inverters. Externally they cannot be distinguished from asynchronous motors, they fit in the housing systems and allow similar combinations with standard gear units either with direct attachment or by attachment with an adapter. Motor-mounted inverters are also possible.
Another step towards a new system, which operates a permanent magnet synchronous motor with an efficiency that corresponds to IE5+ with a frequency inverter has produced further opportunities to reduce power losses: With single-tooth windings, the shortest winding head which is physically feasible with conventional magnetic flux guidance became reality. In addition there was an iron package made from high quality low-loss material according to the principle: Material can be omitted wherever it is not required for flux guidance. This leaves space for the copper winding with low resistance and a compact coil. The frequencies of 200 Hz at up to 3,000 min-1, which are necessary due to the 8-pole design, remain manageable. The optimized rotor contour causes little torque ripple and low cogging torque interference so that the motor is easy to control, even though it has low induction and very fast response. Together with the low-inertia rotor, the user has the opportunity to implement frequent switch-off (start-stop operation) to reduce losses without large energy losses in the masses which are moved.

New Motor Technology with a High Level of Integration
With the new generation of IE5+ motors*, NORD DRIVESYSTEMS takes the step towards a new product system landscape with a focus on ultimate energy efficiency paired with compact design. The size 71 synchronous motor is suitable for the power range from 0.35 to 1.1 kW with a continuous torque from 1.6 to 4.8 Nm and speeds from 0 to 2,100 min-1. Size 90 is suitable for the power range from 1.1 to 2.2 kW with a continuous torque from 6.8 to 10 Nm. With regard to power density, reliability and economy, the new IE5+ motor sets new standards and offers considerable performance advantages that have been further optimized with the latest development of the DuoDrive geared motor, the first IE5+ synchronous motor that has been fully integrated into a single-stage helical gear unit.
*based on the efficiency classification as per IEC60034-30-1 and IEC 60034-30-2