Focus on TCO: How you can reduce costs and increase efficiency at the same time with the right strategy
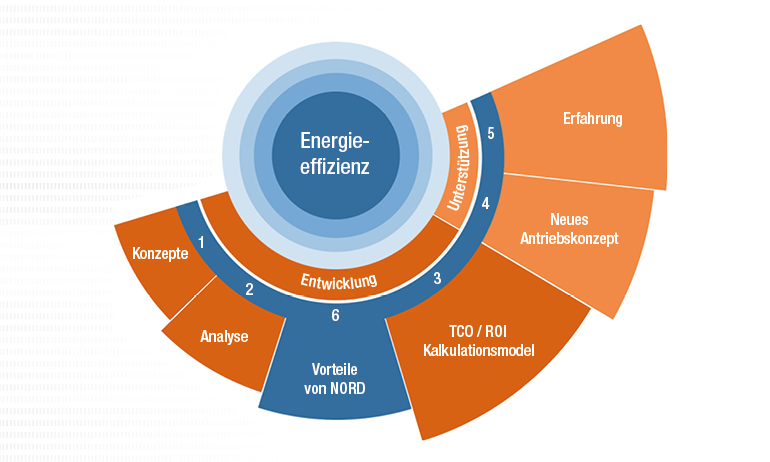
Did you know that the right drive technology can help to significantly reduce your Total Cost of Ownership (TCO)?
Efficient drive technology is the motor for progress. But anyone who looks solely at the purchase price when making an investment decision and disregards the follow-up costs is making a crucial mistake. After all, 80 to 85% of the Total Cost of Ownership is distributed on downstream processes, e.g. for electricity consumption, administrative processes, service and maintenance, spare parts stocking or disposal. Careful consideration of all economic aspects is therefore absolutely essential. The concept of Total Cost of Ownership (TCO) provides support in this respect. We will show you how you can reduce costs and increase system efficiency at the same time with the right strategy.
Cost reductions and efficiency increases in production: That is the goal of all investments. Drive technology plays a decisive role in this. After all, according to studies, the consumption of electric drives amounts to up to 70% of the industry’s total energy consumption. Nevertheless, many users still focus mainly on the purchase price when making investment decisions, although the costs for operation and recycling have a much greater impact. Fact is: If aspects such as energy efficiency, operational reliability, maintenance effort and variant reduction are also taken into account, it pays off in the long term. By using highly efficient technology in combination with a consistent variant reduction and standardisation, the Total Cost of Ownership (TCO) of drive systems can be significantly reduced.

What is Total Cost of Ownership (TCO)?
Total Cost of Ownership is an economical method for the calculation and consideration of all costs incurring along the entire life cycle of investment goods. In addition to the purchase price, this also includes all costs associated with the operation and recycling or disposal. The goal of a TCO analysis is to obtain an overview of all aspects of cost for the use of a product. A TCO analysis is an important tool for investment decisions and profitability calculations, as it reveals cost drivers in advance, uncovers hidden costs, and shows savings potential. A distinction is made between direct and indirect costs. Direct costs can be directly assigned to a product or service and are thus visible at first glance. The determination of indirect costs is much more complex, as they are usually difficult to break down to individual investments.
Benefits of a TCO analysis in the field of drive technology:
- Comprehensive analysis of the installed drives or drives to be installed
- Determination of the energy consumption
- Calculations for the optimal number of drive variants
- Identification of hidden costs
- Evaluation of savings potential
- Careful consideration of all economic aspects
- Targeted design and consideration of the entire system

The life cycle costs of drive systems
So what does this mean for drive technology? What are the direct and indirect costs? How can the Total Cost of Ownership of drive systems be reduced? The life cycle costs of drive solutions include all of the costs incurred – from purchase and commissioning, use and maintenance, up to disposal. The purchase price accounts for only 15% – and should never be the sole decisive factor. Approximately 85% – and thus the majority – result from the downstream processes: energy costs, administrative costs, service and maintenance costs, training and documentation, personnel costs, spare part stocking, failures, and downtimes as well as costs for recycling and disposal. In times of climate change, the sustainability of the overall project is an important aspect of the public image. Acting in a sustainable manner will always have a positive impact on life cycle costs in times of rising prices for raw material and energy.

Increasing efficiency potential
What can operators of a system do? For new systems, they should consider aspects like sustainability and life cycle costs accordingly in the tender criteria. For existing systems, an energy audit is recommended, which will show starting points for specific optimizations. The best basis for an optimum drive design and thus reduced TCO results from intensive examination of the project and its requirements as well as careful consideration of all economic aspects. NORD application engineers therefore support their customers with comprehensive analysis and consulting services right from the planning stage. The North German drive specialist takes a holistic approach to reducing the Total Cost of Ownership, using the full range of optimization strategies for identifying and increasing efficiency potential – from the modular system through the use of powerful, durable, and economical drive technology to the individual TCO calculations and intelligent service and maintenance concepts.
This is what you should look out for if you want to reduce the TCO of your drive systems
Drive technology is the key for reducing the Total Cost of Ownership. The ideal drive system for the customer’s individual application depends on the respective application requirements and ambient conditions and must be precisely determined for each project. In general, some factors can be identified that lead to a fast Return on Investment (ROI) and should therefore be used to reduce TCO.
Drive technology properties that contribute to the reduction of TCO:
- Lowest possible energy consumption
- Constant efficiency over a wide speed and torque range
- High overload capacity
- Great adjustability
- As few gear stages as possible
- Installation positions with minimum oil volume, especially for low ratios (keyword: reduction of churning losses)
- Compact design
- Lowest possible maintenance effort
- High operational reliability
- Long service life
- Usable worldwide
- Variant-optimized design
- Modular system
TCO in the conflicting area of energy efficiency and variant reduction
The two major factors to reduce the Total Cost of Ownership are energy consumption and the number of drive variants used. However, there is a conflict of objectives between the approaches of energy efficiency optimization and variant reduction. Planning a system with drives that are designed for the most energy-efficient operating point leads to optimal investment costs and motors operating comparatively energy-efficiently, independent of their efficiency class. In return, many drive variants must be managed and serviced during the system’s entire life cycle. While a drive concept mainly focusing on saving energy costs leads to a large number of variants, a variant reduction has exactly the opposite goal, namely to provide the required torques and speeds in a system with as few different drive variants as is economically feasible. Thus, costs for administration, service and warehousing can be saved, but the energy costs usually increase. With regard to life cycle costs, a balanced combination of variant reduction and energy efficiency can achieve high TCO reductions – particularly in large intralogistics projects for airports or parcel centers where a large number of drive units are installed.
High-efficiency synchronous motors are the key
A very effective measure for reducing the Total Cost of Ownership is the use of highly effective synchronous motors Thanks to PMSM (Permanent Magnet Synchronous Motor) technology, the motors feature a high and relatively constant efficiency over a wide speed and torque range and thus offer optimum energy consumption performance even in partial load and partial speed ranges – a clear advantage over the conventional IE1, IE2 or IE3 asynchronous technology. Therefore, they are more energy efficient in these operating points and, through a reduction of variants, also keep efficiencies at a high level, even in case of over dimensioning. This results in low Total Cost of Ownership (TCO). Synchronous motors reveal their full potential in applications with a partial load range and low speed ranges, which is the case, for example, in the areas of baggage handling, post and parcel processing. Therefore, significant cost savings can be achieved by using synchronous motors. High cost reductions are achieved over the entire product life cycle.

Comparison: IE3 asynchronous motor and IE5+ synchronous motor
Particularly, IE5+ technology
results in significant TCO reduction. The enormous savings potential becomes especially apparent in direct comparison between a conventional IE3 asynchronous motor (0.75 kW, 83% motor efficiency, right-angle gear unit) and a corresponding IE5+ synchronous motor (0.75 kW, 93% motor efficiency, right-angle gear unit). Considering 16 operating hours per day (4,000 h/a), a saving of approx. 400 kWh/a is possible. This corresponds to 0.15 t CO<sub>2</sub> (emission factor of 366 g/kWh) and approx. 11%. This can be multiplied by the number of drives used (with 20,000 drives, for example, this amounts to 3.000 t CO2 per year). In the partial load range, there is even a saving of 18%. So the higher the part of the drives’ partial load operation in the operating hours of the drives, the greater the energy savings through drive selection, and the better the performance of the modern permanent magnet, efficiency class IE5+ synchronous motors.
IE5+ motor: High power density in a small installation space
Due to the optimized power density, space savings of up to 40% can also be achieved with the compact IE5+ motor compared to conventional asynchronous motors. The same installation space can also accommodate a more powerful motor with higher energy efficiency. For example, an IE5+ synchronous motor (which provides a torque of up to 4.8 Nm) is the same size as the previous IE1 motor producing 1.24 Nm. Due to an efficient use of materials and a compact size, the IE5+ motor generation has a weight advantage of more than 50% compared to IE3 asynchronous motors within the same power range. Additionally, less volume and less weight result in reduced transport costs and are therefore more environmentally sound. The mentioned 0.75 kW motor weighs about 10 kg in the IE3 version, the comparable IE5+ motor only weighs about 6 kg. If a IE5+ motor is delivered from Hamburg to Stuttgart instead of an IE3 motor, the CO2 emissions are reduced by about 120 g per motor. Considering the fact that systems with up to 20,000 drives are not uncommon, as well as the worldwide delivery of many drive manufacturers, this demonstrates that high efficiency motors not only contribute directly to sustainability by reducing electricity consumption but also indirectly, thanks to their smaller volume and weight.

The patented DuoDrive geared motor is a real cost reducer
With the DuoDrive, NORD goes one step further. The patented geared motor integrates an IE5+ synchronous motor into a single-stage helical gear unit, and with a system efficiency of up to 92% achieves one of the highest efficiencies on the market in this power class. Very high system efficiency is also achieved in the partial load range. It is thus future-proof and a real cost reducer. The constant motor torque over a wide speed range allows for consistent variant reduction and reduction of operating costs. Together with the simple plug-and-play commissioning, this results in a significant reduction in the Total Cost of Ownership (TCO) in comparison with existing drive systems. The smooth, unventilated and compact design as well as the quiet running with minimum noise emissions are further important features. Elimination of many wearing parts results in lower maintenance. The DuoDrive is available for powers of up to 3 kW with a continuous torque of up to 250 Nm and speeds of up to 1,000 min-1, and covers gear unit speed ratios of i=3 to i=18. Market-compatible connection dimensions facilitate the replacement and the integration into existing plant designs.
The integration of motor and gear unit has a positive impact on the TCO
By integrating the motor and the gear unit in one single housing, DuoDrive is very lightweight and compact, coupled with very high power density. Numerous wear-prone parts such as radial shaft seals are eliminated, and thus also maintenance efforts and friction losses. Reduced gear meshing and bearing points also play their part. Due to the minimized oil volume, churning losses are also lower. The DuoDrive can be mounted without any modifications using the same oil volume in various installation positions. This leads to an additional reduction in the number of variants. The compact housing dimensions have another advantage: DuoDrive has a slimmer design than competitor products and thus provides for a narrow aisle width in conveyor technology installations. As the geared motor power can be scaled in the same design without modifying the outer dimensions, plant layout modifications are not required for power adjustments.
Low Total Cost of Ownership thanks to targeted variant reduction
In addition to energy consumption, targeted reduction of the drive variants used also offers great potential for optimizing the Total Cost of Ownership. A variant is a combination of gear unit, motor and frequency inverter available in different sizes and gear ratios. Variants may be reduced by using only one geared motor and frequency inverter size for a specific speed and load range. Controlled via the frequency inverter, this drive unit may then cover all required operating points for lower performance requirements or other speed ranges.
Significant cost savings
When reducing the number of variants, project costs tend to rise slightly because larger drives are used in some cases, which leads to additional costs compared to customized dimensioning. In return, however, the operator benefits from optimized operation of their system and significant cost savings in the areas of administration, service and spare parts stocking over the entire service life of the drives. The system integrator also saves costs, for example in engineering, through a systematic variant reduction.
This is how you benefit from a reduction of variants:
- Energy costs: An analysis and consideration of the actual load conditions (keyword: partial load) can achieve permanent energy cost savings. Positive side effect: a smaller carbon footprint.
- Engineering costs: Fewer variants have to be designed and processed in the engineering process. This simplifies the drive selection and visualization of the system.
- Administrative costs: Fewer part numbers and variants have to be managed. This facilitates the maintenance of part lists and reduces the procurement effort. At the same time, fewer incorrect installations or incorrect orders result in lower error costs.
- Documentation costs: Documentation efforts are reduced thanks to standardization and reduction of variants.
- Training costs: Easier maintenance, commissioning and parameterisation also means reduced training effort.
- Spare parts costs: Fewer types of spare parts and fewer parts in stock result in less capital commitment for the spare part stocks and fewer errors in ordering and installation.
- Commissioning, service and maintenance: Standardization, modularity and plug-in capability facilitates maintenance and commissioning as well as repairs. Service intervals and measures become easier to plan, and plug-and-play installation saves a lot of time and effort. Additionally, there is excellent support from the NORD DRIVESYSTEMS global service network.

LogiDrive: Standardized geared motor variants
Standardized geared motor variants such as the LogiDrive drive systems
from NORD are perfect for variant reduction and enable significant reduction of costs over the product service life (Total Cost of Ownership – TCO). LogiDrive is an energy-efficient, service-friendly, and standardized modular system. Depending on the industry and objective, different NORD products are combined to create a drive solution that is 100% tailored to the respective requirements of conveyor applications in the fields of post & parcel and airport as well as warehouse. All LogiDrive systems are efficient and extremely easy to maintain and install thanks to plug-and-play technology. Utilizing the high overload capacity of the motors and the system’s wide adjustment range, they are individually tailored to each customer and specifically designed for the system’s individual load range.
Find out more about TCO
Would you like to find out more about how drive technology can help you reduce your Total Cost of Ownership? Download our white paper “Total Cost of Ownership: Drive technology is the key for reducing the Total Cost of Ownership” and find out more about savings potential, optimization options and how NORD realizes TCO reduction.