Jütro Feinkost
Intelligent, balanced, stable: Drive technology ensures safe operation
Jütro GmbH & Co. KG Konserven und Feinkost from Jüterbog in Brandenburg is a traditional as well as future-driven family company with 150 employees. It was founded in 1911 and is thus a pioneer in canned products technology. In 2021, Jütro has established a new PET bottling plant in cooperation with NORD DRIVESYSTEMS and other partners, where geared motors, frequency inverters and application expertise play a leading role.

Focus on the Customer
In the first decades, its proximity to the Spree Forest made the company focus on gherkins processing. As the complete company name reveals, Jütro is now specialised on the gentle development and preparation of premium shelf-stable food such as home-made spicy stock, soups and sauces or creamy basil mayonnaise. The comprehensive convenience range includes more than 400 products. Whether a new recipe or the refinement of classics: Jütro goes in for ultimate quality for all ingredients and production stages. This is also required in the large trade brand product range, that Jütro supplies “just in time” with full traceability, on schedule and in compliance with strict quality standards. All production plants must therefore be fully available, while unplanned failures and downtimes are to be avoided by using reliable technology and optimal maintenance of all plant components.
The best for the brand- Where Jütro makes no compromises on quality and taste, its packaging range is flexible: Whether glass or PET: various packaging types and sizes are possible. For this purpose, ultra-modern bottling systems for small and large bottles are available. The range has now been expanded with another bottling line for PET bottles. Jütro as well as its sister company Elbak in Greece have been cooperating with NORD DRIVESYSTEMS, and great confidence in quality and efficiency of the NORD drive technology has grown. So it was already quite clear that NORD DRIVESYSTEMS from Bargteheide would handle the order for a new bottling and packaging line, and equip it with the right drive units. The complete bottling and packaging technology was delivered by other project partners, including two companies from Germany, one from Spain and one from Italy.
The brand-new PET bottling plant bottles ketchup, remoulade sauce, mayonnaise and salad dressings at high speeds. The high market demand necessitated the investment. As it is increasingly difficult to find sufficiently qualified personnel, the highest possible level of automation and throughput was planned from the very start. Depending on the product, 150 bottles can be produced per minute. This is 70,000 bottles in one shift. To achieve this number, an optimally balanced production process is required.

Project Challenge
Ethernet connection allows complete online maintenance - “Jütro came up with the request for stable drive systems comprising an intelligent solution for the frequency inverters. The frequency inverters should also be Ethernet-integrated to allow for remote maintenance tools and similar applications”, Jan Huesmann, Business Development Electronic Drivesystems at NORD outlines the project’s key points. The NORDAC PRO SK 550P frequency inverter was selected as a machine inverter design with Ethernet connection and for power output from 0.25 to 1.5 kW to allow the suppliers of the different plant components to maintain the frequency inverters with remote control support via Ethernet. Via online maintenance, they can inspect the entire system, check for faults and evaluate all data from the NORD frequency inverters for their plant sections.
Precise drive control for all conveyor applications - In the first plant section, the empty and very lightweight PET bottles are brought into line and placed upright. Here, it is particularly important to precisely adjust the speeds via the frequency inverters to avoid any faults caused by bottles falling over during conveyance. The transport routes between the stations are equipped with normal worm gear motors.
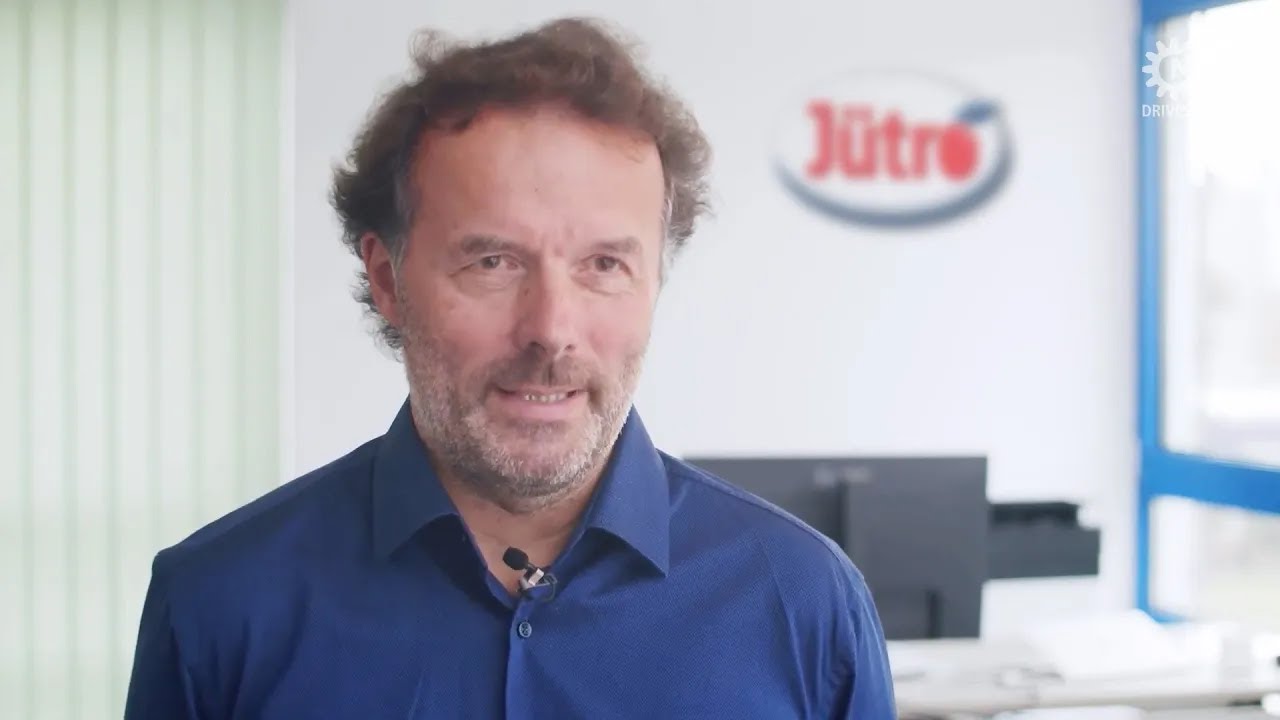
Application Solution
Intelligent automation is essential - In the further process, the bottles are sealed and packaged. Here, it is particularly important to run the system with high speeds and to control the conveyor line drives in a much coordinated manner. A task, the NORD frequency inverters perform very well. “From bottle preparation to bottling and packaging, drive units with frequency inverters by NORD DRIVESYSTEMS are used in every machine and perform various tasks such as product transport, sealing and packaging. We are very satisfied”, Retzke explains.
Dieter Kohrs, HR manager at Jütro GmbH & Co. KG explains: “Our focus is on automation, as the continuous running of our systems is of great importance to us. This is why the entire technology and here especially the drives must be well balanced, and it is of utmost importance that they have a high level of stability.”
The NORDAC PRO SK 550P control cabinet inverters from NORD are very compact and space-saving, and have an integrated Ethernet interface via which up to seven additional frequency inverters can be integrated in the higher-level control via CANbus, without these seven frequency inverters each requiring a separate Ethernet port – a clear cost advantage. At Jütro, PROFINET is used as one of the four Ethernet protocols integrated in the NORDAC PRO SK 500P. Furthermore, the vector regulation of the frequency inverters was used in this project to keep the speeds constant. Speed variation was used as well as the control via analogue inputs to pass different speed controls. Thanks to the data modules and device files provided by NORD, the different partners could easily implement the automation strategy with regard to drive technology – another clear cost and practical benefit.
Good service: competent, practical, fast - Dieter Kohrs: “The service from NORD has been very convincing – fully competent and perfect. We were very pleased with the clearly, practically and quickly proposed solutions, which we were able to implement without problems. Some partner companies, for example in the bottling field from Italy, confirmed this.
We at Jütro agree to further invest in automation and consider this absolutely necessary. At the moment, we are considering a new overall concept for final palletising, which is currently done manually." For Kohrs, it is clear: “We have to continuously increase the efficiency of our plants, always asking ourselves: Does it get faster? Does it get safer? Does it get better? Of course, NORD is back in the running as a potential project partner.”
유니케이스 웜 기어 유닛
조용하고 강력
UNIVERSAL SMI 윔 기어 유닛
낮은 소음 및 매끄러움
UNIVERSAL SI 웜 기어 유닛
모듈식 유연성
Find further information here: